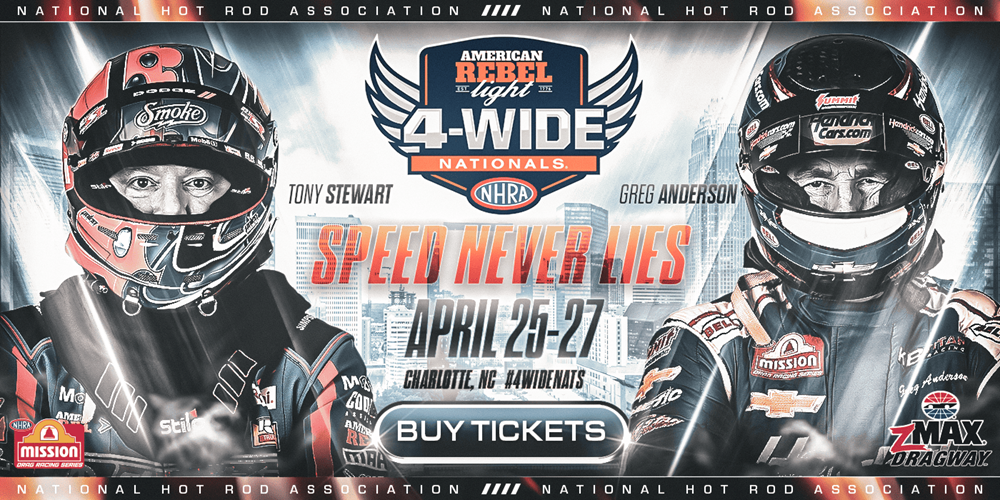
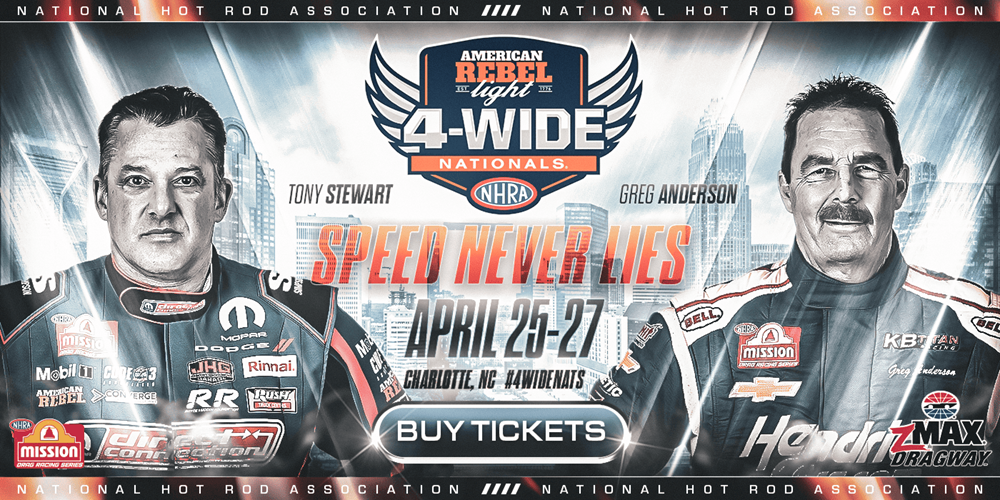
Fuel System 101: The basics of how to keep your beast fed a healthy diet
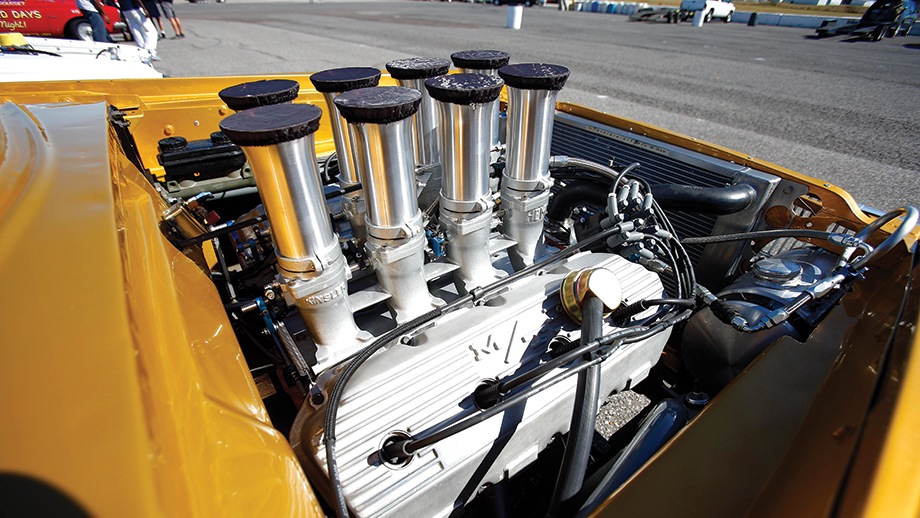
Fueling your engine is one of the most critical processes in racing. From idle to wide-open throttle, the range of ideal fuel-delivery scenarios requires a fuel map that can cope with every possible running condition. And for those who drive on the street or around the pits, drivability is essential. Whether you’re running a carburetor or fuel injection, the goal will be to dial in the most efficient air-to-fuel ratio and have the ability to tune for varying conditions. To do this, you’ll need a fuel system that is up to the task.
In designing a system for your vehicle, you’ll start with the tank or cell and consider the pump and filter(s), lines, rails (when applicable), regulator, and injectors or carburetor. Many of these parts are expensive, so you’ll want to get it right the first time.
With that, let’s look at fuel pumps and what the experts have to say. We spoke to Evan Perkins, digital content manager at Holley; James W. Kinsler, vice president at Kinsler Fuel Injection; and Jim Craig, product manager at Weldon High Performance.
“The two most important aspects of fuel pump selection are going to be flow rate and pressure requirements,” said Perkins. “A fuel pump may be able to flow enough fuel to make 1,000 hp on a carbureted application but fall short at that same power level when delivering higher fuel pressure requirements for electronic fuel injection [EFI]. Other considerations for fuel pump selection are fuel compatibility, which is an important conversation with the increasing prevalence of ethanol and methanol in racing, and fuel pump packaging.”
Craig added, “The most important factors to consider are: engine size, carb or EFI application, power adder if used, fuel type, and if there are any restrictions on the type of fuel pump required — electric or mechanical. I can initially determine the appropriate pump, electric or mechanical, by asking about the class the car is being raced in and narrow the recommendation easily from there.
“The basic fuel consumption calculation used estimates 10 gallons of fuel per hour [gph], which supports 100 hp. So, a 1,000-hp Super Stocker, for example, would require, at the minimum, a fuel pump that will move 100 gph at the required system fuel pressure [example: carb at 30 psi or EFI at 60 psi]. In addition, generally, a 30% to 40% cushion is added to the requirement to allow for the system and application.”
Taking a deeper look, Kinsler expanded on the question. Kinsler says to start by calling a retailer who has a very competent technician you can speak with. “He will need to ask you about 10 to 15 questions to spec the right pump for you, but you will be likely to obtain the correct pump. The wholesale ask-no-questions places are less expensive, but if you install the wrong pump, the cost savings may cause you much aggravation and possibly even engine damage. Another good approach is to ask racers who are running strong with a similar engine, as they are usually glad to help.”
Kinsler added, “On a very hot day, with a low barometric reading or a higher altitude, it is very common for a pump of any design [electric or mechanical] to pump significantly less than its rated output flow, due to boiling of the fuel in the inlet line and in the internal pumping segments. All pumps should be at 20% higher flow than the engine needs. Some customers insist on just 10% or 15% extra flow, and we see some of them having problems. The customers are concerned that pumping the extra flow heats the fuel slightly, but that additional heating is negligible compared to the heat picked up by fuel lines run in hot areas or the fuel tank’s exposure to the hot pavement or the sun.
“Electric pumps are much easier to install than mechanical pumps, which require a timing belt drive off of the crank and a location close to the crank; sometimes, there is barely enough room. One advantage of a mechanical pump is that its output flow increases about proportionately with engine speed, as does the engine’s horsepower curve, so it can be about what the engine wants through a wide rpm range. We offer a super-premium mechanical pump.”
Here’s how Kinsler Fuel Injection says it separates its pump design from the rest of the industry. First, it constructed a six-station pump durability bench with a flow meter accurate to 1/10 of 1% at any reading. Micro Motion makes these meters in Boulder, Colo., at about $12,000 each. Most good instrumentation is about 1/4 of 1% of full-scale error. This means if the flow meter reads 400 pounds per hour [lb/hr] full scale, then the error at any reading is 1/4 of 1% of 400, or 1 lb/hr. This isn’t bad at 400 lb/hr, but at 5 lb/hr, it is still 1 lb/hr; a potential error of 20%. At 5 lb/hr, the Micro Motion is off just .005-pound. Kinsler invested in precision pump speed controls and flow and pressure measurement to see exactly how well its pumps flowed.
“The latest pumps have a seal design that can’t leak externally and have one of the side plates loaded by outlet pressure against the side of the gears to cut the internal leakage to a minimum, which gives improved pump performance. Every pump gets flow tested, run in on a varying speed and pressure cycle for two hours, then reflowed before being shipped.
“We now have 4,600 Kinsler Tough Pumps in the field without failure. The pumps sell for about $1,000 compared to our closest competitor’s at about $550, but we spend a lot more money making each part in the pump.” Kinsler states its pump will live at a higher pressure than others it has tested; 200 psi for sprint car use, and 300 psi or more for drag racing. “Some teams send in their pumps each winter, and most all of them look close to new,” added Kinsler. “And you can look at Kinsler.com to see the Tough Pump features.”
Kinsler continued, “Some electric fuel pumps are extremely well made, and a few brands offer variable output flow controlled by the ECU, which can be very handy to obtain an exact fuel map. The biggest culprit that hurts an otherwise premium electric or mechanical fuel pump is dirt, both causing wear and plugging up injectors and pressure relief valves in EFI systems. You must run a filter on the inlet of every pump to protect it. We recommend a 70- to 100-micron stainless steel mesh filter on all the mechanical fuel pumps and a 45-micron stainless mesh on the electric pumps.
“You must never run an inlet filter with a cellulose [a fancy name for paper] element.
“Too often both gasoline and alcohol have some moisture in them, which is quickly absorbed by the cellulose fibers, causing them to swell, which closes down the openings in the filter material, causing a restriction, which is a major no-no for the inlet of the pump. We do like a cellulose filter on the outlet of the pump for all EFI systems. See our 10/3 element featured right at the top of our home page at Kinsler.com as 95% of the NASCAR Cup cars run this filter; it is close to magic.”
Another decision you’ll need to make is whether to run an in-tank or external fuel pump. This question has more to do with electric pumps, since mechanical pumps will generally be externally mounted in the engine compartment.
“We highly recommend in-tank pumps, especially in EFI applications,” said Perkins. “In-tank fuel pumps run cooler, which extends pump life, and the fuel also helps to muffle any noise created by the pump for a quieter ride.”
Kinsler added, “The best thing about a pump inside of the fuel tank is that it is cool. Production car tanks are very carefully designed to keep the fuel at the inlet of the pump. Most racer-made tanks are marginal at best. The most common problem is the tank is not designed to keep the fuel at the inlet of the pump. It moves away in turns, and the pump sucks air. If you mount the pump outside of the tank, keep it as close and low as you can so the fuel will flow properly and cover it with insulation. It is best to insulate all of the fuel lines that run through a hot area. One big advantage of an externally-mounted pump is that it can be quickly replaced. And don’t use any cross-drilled angled AN fittings in the pump inlet line; make all the required bends on the inlet side of the system with hoses or with a large-radius bent-tube fitting.”
“For most, if not all, drag racing applications, I do not recommend in-tank fuel pumps,” said Craig. “While Weldon offers a fuel pump series that can be mounted in-tank, it’s clean, and it’s compact, but the pump takes up space within the fuel cell that would be better served to have fuel in its place. Our fuel pumps are known to suck or draw fuel, almost as well as they push fuel, so we don’t worry too much about having the fuel pump out of the cell; beside it, behind it, or above it.” Carburetor vs. EFI
Not all pumps are created equally, but are there differences between pumps designed for carburetors and EFI? “The main difference is the pump’s maximum outlet pressure,” said Kinsler. “Most carburetor systems run about 12 psi at the carb, so that pump doesn’t have to be made as precisely as one for an EFI system, which might range from 35 to 130 psi at the fuel rail. The pressure to a carburetor is usually controlled by a pressure regulator valve, placed directly in the fuel line going from the pump to the carb, essentially ‘holding back’ the fuel that isn’t needed.
“To keep from causing the pump outlet pressure to rise too high, most pumps for carbs use an internal pressure relief valve set at a few psi over what the pressure regulator valve is set to. All production cars have pressure regulator valves because it makes a less expensive system, not having a line going back to the fuel tank. One disadvantage of this system is that very little fuel flows to the fuel pump at an idle or low engine speed. Vapor can build up in the line from the fuel tank to the pump, causing vapor lock.
“Pumps for EFI systems must make more pressure, so they have a larger motor and draw much more current. In any car that sits out on the hot pavement on a warm day, the fuel in the EFI hoses and rails can boil, and that makes bubbles in the system. To purge the system of air bubbles, all the pump output fuel is sent directly to the fuel rails. A pressure relief valve [PRV] relieves fuel from the outlet of the fuel rails and sends it back to the fuel tank to control the pressure in the system. Designed properly, this system works quite well and is never subject to vapor lock.”
Kinsler continued, “Keep in mind, both kinds of valves are pretty sensitive to dirt, but especially the pressure relief valve. All EFI injectors and pressure relief valves should have 3-micron filtration, referring to the nominal diameter of the holes that pass through the filter material. One-thousandth of an inch is 25.4 microns, so 3 microns is .000118 of an inch, or just over 1/10 of a thousandth. No EFI injector manufacturer recommends 3-micron filters because they plug up too quickly; they all recommend 10 micron, which is too coarse. The problem is, if an EFI injector or a PRV closes down on a small particle of dirt, it will often stick to the seat or the valve head and cause leakage through the valve.”
“In a more simple explanation, Perkins said, “EFI pumps, by requirement, are designed to produce higher fuel pressure, typically above 40 psi, to support modern fuel injection systems. Carbureted pumps tend to produce fuel pressure below 15 psi. However, with proper fuel pressure regulator selection, Holley offers many pumps that can support both applications.”
And Craig added, “For Weldon, it wasn’t until a few years back that we offered a specific fuel pump for carb usage. What we did offer was a separate fuel pump that could support either carb or fuel injection applications. The pressure was dictated by the correct bypass regulator. In the ’90s, we supplied a fuel pump that was found on most of the GM Pro Stocks, which used a bypass regulator to maintain the correct pressure for the carbs. That same pump, using the same style bypass regulator with a heavier spring, is able to support more than 2,600 hp at EFI pressures. So, the actual pump mechanism is the same: You manipulate the fuel pressure using a properly rated bypass fuel regulator.
“Weldon offers a series of fuel pumps that use an integral bypass regulator, and which are for use only with carburetion. While the pump element itself can and is used in EFI pumps, the motor and body assembly are not designed to support EFI fuel pressures.” Building a Pipeline
With the proper pump selected for your horsepower level and specific application, you’ll need to determine the correct lines to connect the pump to the engine.
“There are plenty of hard rules in place when it comes to sizing lines and fittings, but if a racer is unsure of whether his fuel system is up to snuff, data-logging is an excellent way to make certain,” said Perkins. “If the fuel pump is rated to deliver sufficient flow and pressure, the regulator is set correctly, and the fuel filter(s) is correctly sized and clean, recording the fuel pressure during a pass will clearly show a pressure drop indicative of a problem. We also encourage racers to use high-quality fittings, such as those from Earl’s, that incorporate smooth internal radii for improved flow. There are many inferior fitting and hose end designs that neck down considerably and can impede flow.”
Craig added, “For fuel pumps that flow up to 100 gph, a -8 AN [1/2-inch inside diameter] is sufficient for both the feed line and supply line to the motor. For fuel pumps [more than] 100 gph and under 200 gph, at a minimum, a -10 AN [5/8-inch] feed line to the pump and supply is suggested. [More than] 200 gph, then a -12 AN [3/4-inch] feed line to the pump and a -10 AN supply to the motor is required. If the application is using a carburetor with the bypass regulator at the front of the vehicle [fuel pump in the back], then you must always go up one size on the return line. If you are feeding the carb with a -10 AN line, then you need to return with a -12 AN line to ensure the proper pressure control.
“As to fittings, always go with the high-flow-style port adapters. Refrain from using any hard 90-degree or cast fittings in a fuel system to prevent cavitation and restrictions in the system. And avoid using swivel-type fittings on the inlet side of the fuel pump/filter assembly to minimize the chance of cavitation or restriction.”
Kinsler said emphatically, “Any type of fuel pump needs an excellent supply of fuel to it and to the engine. Mount the pump as close to the tank as you can, as low as you can, in as cool a spot as you can, with no angle fittings in it at all. Just make the bends by bending the hose. Refer to the picture for the tightest fitting bend that Kinsler is comfortable with. Most blue anodized fitting forgings have nice radii on the outside, but look on the inside. A 90-degree fitting is made by two drills intersecting with a razor-sharp inside corner, so this can cause tremendous cavitation and is a vapor bubble generator – a real fuel system killer.” Inspection and Maintenance
Like any system in your car, your fuel system deserves a regular inspection. Pumps, lines, and regulators are not items you want to leave to chance, and they can be a pain to work on at the track. With that, you should check your equipment on a regular schedule to ensure peak performance.
“Inspection of the fuel pump system is always a good idea in the offseason, but in certain applications can be needed much sooner,” said Perkins. “In the case of E85 or higher percentage, ethanol-based fuels, inspection and service can be needed often. Ethanol is very hard on fuel system components, especially aluminum, and can quickly eat certain hose and filter media types, making proper component selection key. It is also hydrophilic, which means it attracts moisture. This moisture can cause rust in steel tanks and other fuel system gremlins, especially if stored for long periods of time in the vehicle’s fuel system. We highly recommend draining the tank if ethanol-powered vehicles are going to be stored for any period of time.
“One of the most common mistakes we see in fuel system designs is using an incorrect filter. A filter lacking adequate flow can mimic other engine problems and is often very hard to diagnose. For EFI applications, we recommend a 100-micron fuel filter between the tank and the fuel pump, and a 10-micron filter before the fuel rails.”
Craig added, “At a minimum, the fuel system should be inspected before the first race of the season. This will include either cleaning or replacing the fuel filters in the system. Check the fuel line(s) to make sure there are no kinks, soft spots, or damage. If a racer has tie-wrapped something to the fuel line [return line, brake line, etc.], make sure that it isn’t crushing the line in those areas. You will also need to inspect the tank vent for any restrictions or damage. Tanks are typically vented to the outside of the vehicle and should have a small filter or breather placed on them to prevent contamination from finding its way into the fuel.
“Ideally, when using a non-oxygenated fuel, once the season is finished, keep at least enough fuel in the system to cover the fuel cell foam [if used], the fuel pump assembly, and any associated filters. This prevents those items from drying out and becoming damaged. If the fuel is oxygenated, then it has to be purged from the system and then flushed with a good grade of non-oxygenated fuel so that everything in the system is now full of that new, clean fuel. It is also a good idea to add a fuel treatment product to the fuel to keep it fresh and prevent moisture build-up.
“As to servicing a fuel pump, if the filters are kept clean, the fuel kept free of contaminants, and the system never allowed to dry out, a pump should never require service — at least not a Weldon,” he said. “Filters should be serviced or replaced at least once per year or if the vehicle sits for a longer than normal period. Do change the filters, especially if the system dried out or was left open.” Common Mistakes to Avoid
Size the fuel pump for the application and the system will be better off. Adding too small a fuel line, either from the tank to the pump, or from the pump to the carb or fuel rails. Installing too small a fuel line on the return on either a carb or EFI application. Going with too restrictive a fuel filter (pump inlet or outlet). Like fuel line fittings, not all filters are the same, even though they might be in the same sized housing.
Improper electrical connections will kill a fuel pump, and you also need to have the properly sized relay powering the fuel pump. Too often, a relay isn’t used, or if one is, it is placed too far from the pump, resulting in reduced voltage to the fuel pump motor, which reduces flow and places an additional load on the motor. Contaminated fuel is an issue due to either dirt or moisture or even old fuel that has broken down.
And one final issue for consideration is the fuel tank vent. The tank vent needs to be sized for the fuel pump being used. Ideally, a 3/8-inch tank vent is fine for most fuel pumps, but for some large displacement units, a 1/2-inch vent would be ideal.